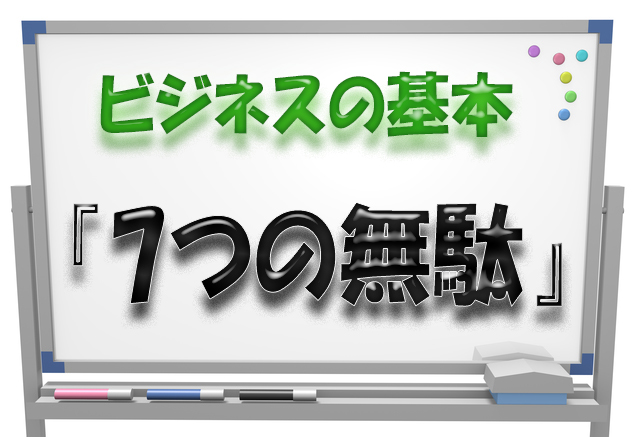
現代のビジネス環境では、限られた資源を最大限に活用し、生産性を向上させることが求められています。その中で、トヨタ生産方式(TPS)に由来する 「7つの無駄」 は、多くの企業や組織で活用されています。本記事では、「7つの無駄」の概要と、それを削減するための具体的な対策について解説します。
『7つの無駄』とは?
「7つの無駄(Seven Wastes)」とは、トヨタ生産方式(TPS)の基本概念の一つであり、生産活動の中で発生する 不要な作業や資源の浪費 を指します。これらの無駄を削減することで、 コスト削減・品質向上・納期短縮 などの効果が期待できます。
7つの無駄の種類:
- 過剰生産の無駄
- 手待ちの無駄
- 輸送の無駄
- 加工の無駄
- 在庫の無駄
- 動作の無駄
- 不良・手直しの無駄
それぞれの無駄と改善策
過剰生産の無駄
無駄の例:
- 実際の需要を超えて製品を作りすぎる
- 余計な在庫が増えることで管理コストが増加
改善策:
- ジャストインタイム(JIT) の導入(必要なものを必要な時に生産)
- 需要予測を正確にし、生産計画を最適化
手待ちの無駄
無駄の例:
- 作業員が材料や指示を待つ時間
- 機械のメンテナンス待ち
改善策:
- 工程間のバランス調整(ボトルネックの特定と改善)
- 標準作業の導入 による効率化
輸送の無駄
無駄の例:
- 不要な輸送や長距離の移動
- 物流の手間が増えることでリードタイムが長くなる
改善策:
- レイアウトの最適化(作業場や倉庫の配置を工夫)
- 輸送回数の削減(まとめて配送する、近隣の仕入先を活用)
加工の無駄
無駄の例:
- 本来不要な工程を追加する
- 過剰品質の要求
改善策:
- シンプルな設計を採用(必要以上に複雑な仕様を避ける)
- 標準化の徹底 により不要な加工を減らす
在庫の無駄
無駄の例:
- 必要以上の原材料や部品を持ちすぎる
- 倉庫スペースを圧迫し、管理コストが増加
改善策:
- 在庫管理システム(ERP)の活用
- 適正在庫の維持(需要予測と連携)
動作の無駄
無駄の例:
- 不必要な動きが多い作業
- 工具や部品を探す時間
改善策:
- 5S(整理・整頓・清掃・清潔・躾)の実施
- 作業の標準化 により無駄な動きを減らす
不良・手直しの無駄
無駄の例:
- 不良品の発生による手直し作業
- クレーム対応に時間を取られる
改善策:
- 品質管理の徹底(QCサークルの活用)
- ミス防止(ポカヨケ) の仕組みを導入
7つの無駄を減らすメリット
「7つの無駄」を削減することで、以下のメリットが得られます。
✅ コスト削減:不要な作業や在庫を減らし、無駄な支出をカット
✅ 生産性向上:作業効率が上がり、納期短縮が可能
✅ 品質向上:不良品を減らし、顧客満足度を高める
✅ 職場環境の改善:作業がスムーズになり、従業員の負担を軽減
まとめ
「7つの無駄」を意識し、継続的に改善を行うことで 業務の効率化 と 利益の最大化 を実現できます。企業だけでなく、個人の仕事術にも応用できるため、ぜひ実践してみてください。
あなたの職場でも、どんな無駄があるか見直してみませんか?
小さな改善が、大きな成果につながるかもしれません!